Gantry cranes for container handling are vital components in port and terminal operations, as they provide efficient and effective movement of containers between vessels, trucks, and storage yards. These cranes, known for their high capacity, precision, and versatility, are essential for streamlining container handling processes in busy maritime environments. This article delves into the detailed steps involved in the process of gantry crane for container handling, focusing on how these cranes operate, their importance, and the safety measures required to ensure smooth and safe operations.
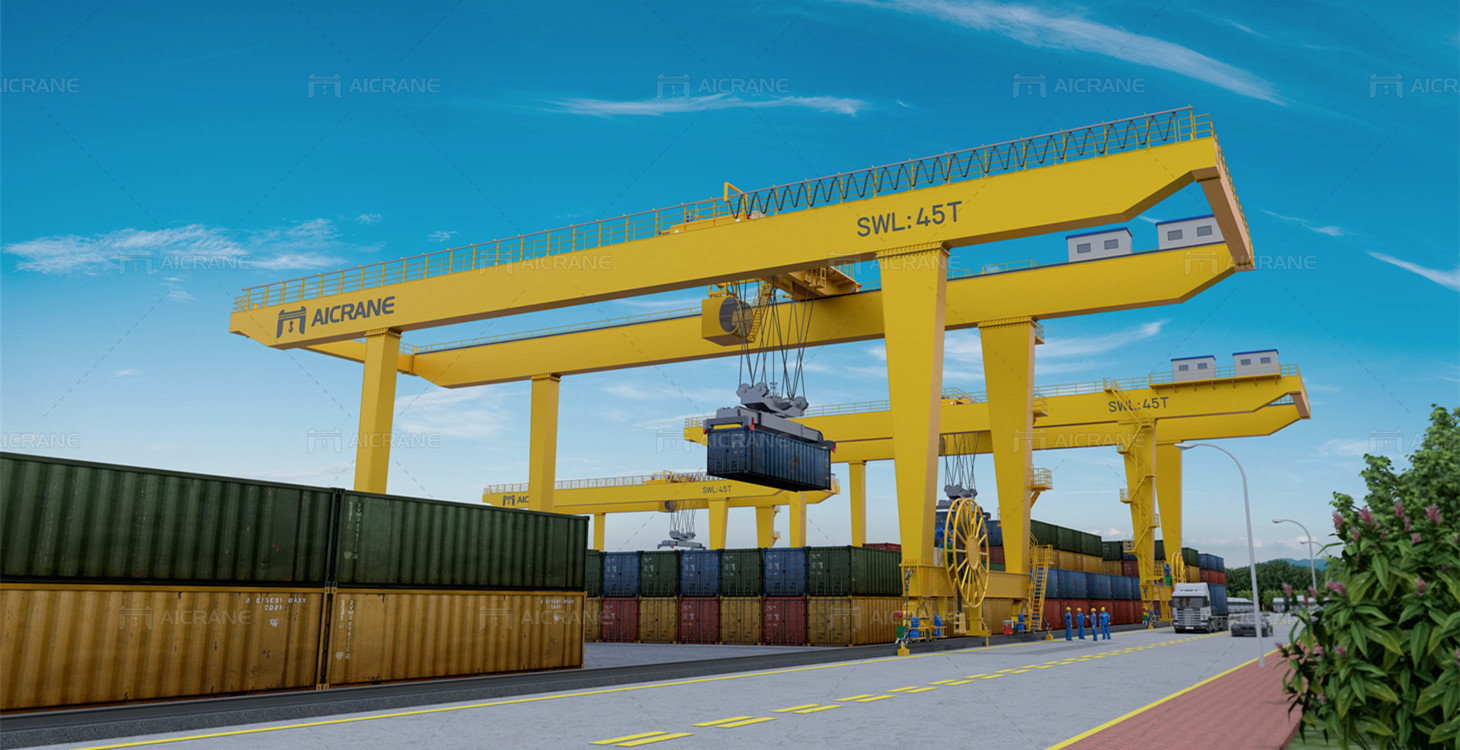
Overview of Gantry Cranes for Container Handling
A gantry crane for container handling, also known as a container gantry crane or container handling crane, is a large machine specifically designed to lift and move containers in port terminals. These cranes typically operate on rails and consist of a horizontal beam, supported by vertical legs, that spans across the container yard or over a quay.
Some key features of container gantry cranes include:
Lifting capacity: Gantry cranes can handle large loads, typically up to 40 tons or more, making them ideal for container handling.
Span and height: These cranes are designed to span multiple containers stacked in rows, allowing for easy loading and unloading of ships and trucks.
Precision and control: Equipped with advanced control systems, gantry cranes provide precise positioning and movement, which is essential for handling containers in tight spaces.
Process of Gantry Crane for Container Handling
Handling containers with a gantry crane involves several steps, from preparing the crane to lifting and moving the containers. Below is a detailed look at each step in the process.
a) Pre-operation Preparation
Before the actual operation of a gantry crane for container handling begins, certain preparations are necessary to ensure smooth operations:
Crane inspection: Operators must perform a thorough inspection of the crane to ensure it is in optimal working condition. This includes checking the hoist mechanism, spreader, rails, and electrical systems.
Load planning: Containers must be planned and organized based on their weight, size, and destination. Proper load planning ensures that containers are stacked safely and efficiently, reducing the risk of accidents and delays.
Area clearance: The operational area must be cleared of any obstructions or unauthorized personnel to avoid accidents during container handling.
b) Lifting the Container
Once the preparation is complete, the gantry crane can start the process of lifting the container. This involves:
Positioning the crane: The crane is positioned over the designated container, which is usually stacked in rows in the container yard or on a vessel.
Lowering the spreader: The crane’s spreader, a rectangular frame designed to lock onto the container’s corner castings, is lowered onto the container. The spreader is equipped with sensors to detect when it is properly aligned with the container.
Securing the container: Once the spreader is in place, it locks onto the container’s corner fittings, securing the load. The crane operator must ensure that the container is fully secured before lifting.
Lifting the container: The container is then lifted vertically by the crane’s hoist system. It is crucial to lift the container steadily to avoid any swinging or sudden movements that could destabilize the load.
c) Transporting the Container
After lifting the container, the crane transports it to its designated location, which could be on a ship, truck, or another location in the yard. This step involves:
Moving along the rail: The gantry crane travels along its rails, moving the container to the desired spot. Depending on the setup, the crane may need to cross over several rows of containers or tracks.
Adjusting the height: During transport, the crane operator may need to adjust the height of the container to clear obstacles such as other stacked containers or trucks.
Monitoring load stability: As the crane moves, the operator must continuously monitor the stability of the container. Some cranes are equipped with anti-sway technology to minimize load oscillations during movement.
d) Placing the Container
The final step in the process is placing the container in its designated position. This could be on a truck, in a storage yard, or directly onto a ship:
Lowering the container: The crane operator lowers the container slowly and steadily, ensuring that it is aligned with the desired location (e.g., on a truck bed or ship deck).
Unlocking the spreader: Once the container is securely in place, the spreader’s locking mechanism is released, and the spreader is lifted off the container.
Final adjustments: The crane operator may need to make minor adjustments to ensure that the container is positioned correctly and is stable.
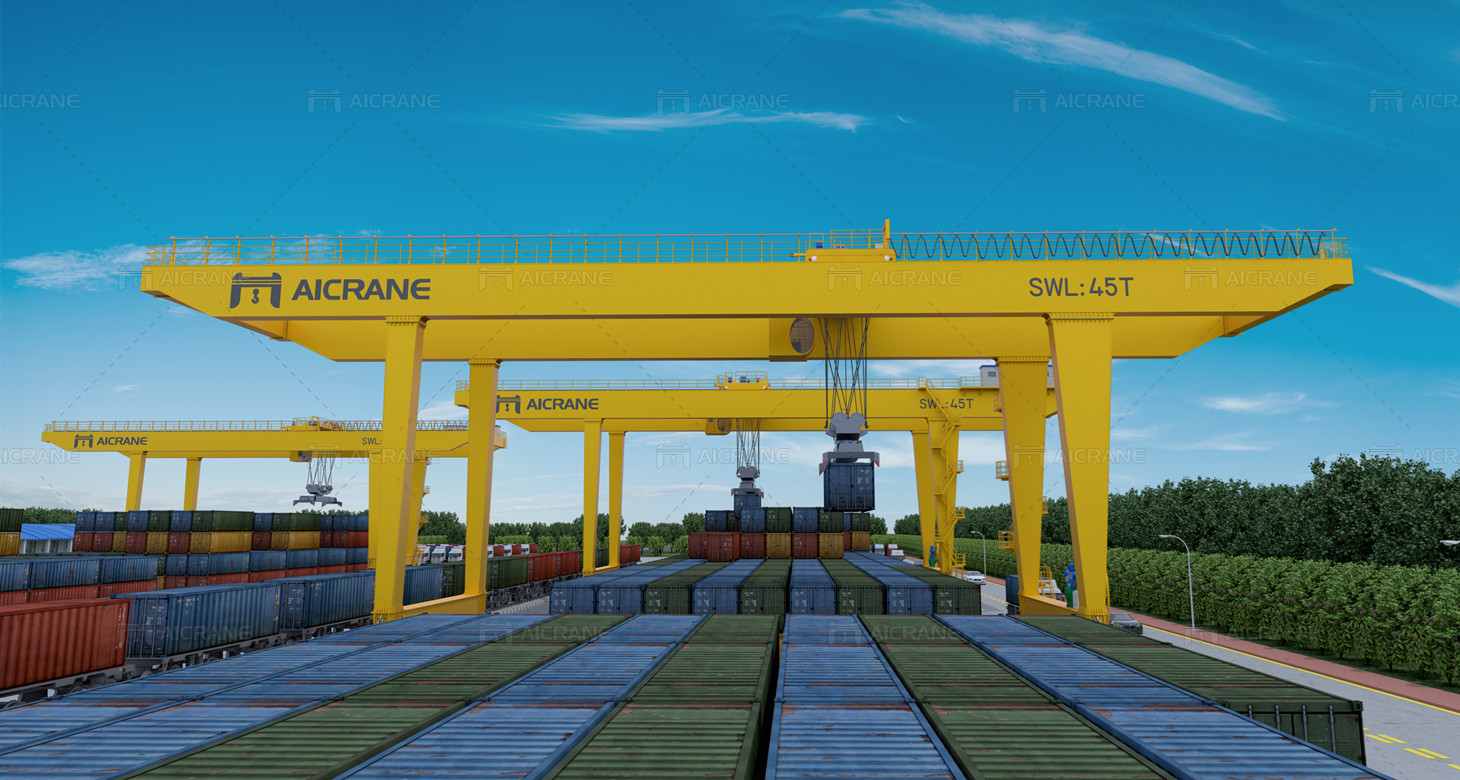
Types of Gantry Cranes for Container Handling
Gantry cranes used for container handling come in various designs, each tailored to specific operational requirements. The most common types include:
Ship-to-shore (STS) gantry cranes: These cranes are used to load and unload containers from ships. They are mounted on rails and can span the width of large container vessels, making them ideal for port operations.
Rail-mounted gantry (RMG) cranes: These cranes operate on tracks and are primarily used in container yards for stacking and moving containers between storage areas and transportation modes.
Rubber-tyred gantry (RTG) cranes: Unlike RMG cranes, RTG cranes are mobile and can move on rubber tires. This makes them flexible and ideal for terminals where rail tracks may not be available or for container yards with limited space.
Key Safety Considerations
Operating a gantry crane for container handling involves significant safety risks, given the size and weight of the loads involved. Adhering to safety protocols (provided by manufacturer like Aicrane) is essential to prevent accidents and ensure smooth operations. Some key safety measures include:
Operator training: Crane operators must undergo rigorous training to understand how to operate the crane safely and efficiently. This includes knowing how to control load sway, respond to emergency situations, and follow safety guidelines.
Load capacity checks: Every crane has a specific load capacity, which must not be exceeded. Overloading the crane can lead to equipment failure or accidents.
Regular maintenance: Routine inspections and maintenance of the crane are critical to preventing mechanical failures. This includes checking the hoist, rails, spreader, and electrical systems.
Clear communication: Effective communication between crane operators, ground personnel, and other workers is essential for coordinating movements and ensuring the safe handling of containers.
The process of using a gantry crane for container handling is a complex yet efficient method for moving large volumes of cargo in ports and container yards. From lifting to transporting and placing containers, each step requires careful coordination and attention to detail. By adhering to proper operational procedures and safety protocols, gantry cranes can greatly enhance the efficiency of container handling, making them an indispensable asset in global shipping and logistics industries. Whether it’s a ship-to-shore crane or a rail-mounted gantry crane, the right equipment and trained personnel ensure that containers are handled with precision, safety, and speed.